Case Study
Cryogenic Service
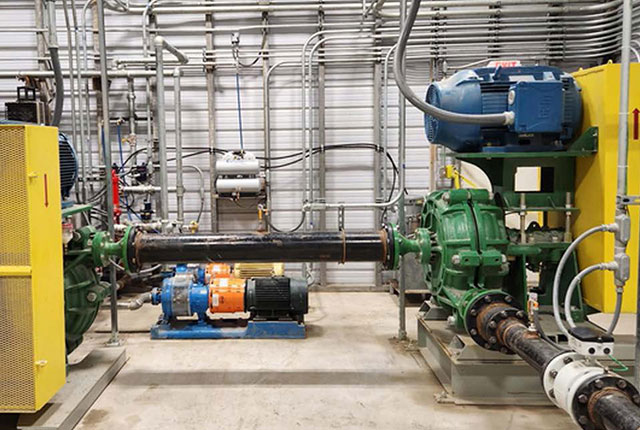
Product: Liquid Oxygen, Nitrogen, Argon, and Hydrogen
Temperature: -175°F to -425°F (-115°C to -253°C)
Pressure: 30 to 50 psi (2.07 to 3.45 bar)
Challenge:
A major manufacturer of industrial and cryogenic gases was struggling to find a reliable sealing solution for their ACD® cryogenic machinery. The original sealing method – using formed bellows and a composite stationary-tometal seal face combination – was short-lived and unreliable in the -175°F to -425°F operating conditions.
The pump manufacturer reached out to Flex-A-Seal for our assistance in finding a solution. Our first project was to seal Argon – the heaviest of the liquified gases produced at the facility. When our cryogenic seal design proved successful, the end user quickly gave us the pump and process specifications to address the remaining equipment.
Solution:
The foundation of the Flex-A-Seal design was an engineered edge welded bellows seal and our first action was to upgrade the materials of construction to accommodate cryogenic temperatures.
A 347 stainless steel welded bellows core did not become brittle in the extreme cold and as a result, supplied greater operating flexibility than the formed bellows. An optimized face combination of tungsten carbide and cryogenic-grade carbon graphite maximized PV values and minimized the face closing load, lowering any generated heat near volatile fluids and gases. A film-forming additive to the carbon enabled self-lubricated operation in the extreme low temperature environment.
Flex-A-Seal also worked closely with the maintenance engineers at the facility to create an in-house rebuild department, ensuring the seals could be repaired to the precise operating conditions.
Result:
The manufacturer not only saw increased MTBF, but the daily operational cost of labor and maintenance to the seals was significantly reduced. And 20+ years later, the end user continues to use Flex-A-Seal’s cryogenic solutions in their facilities.